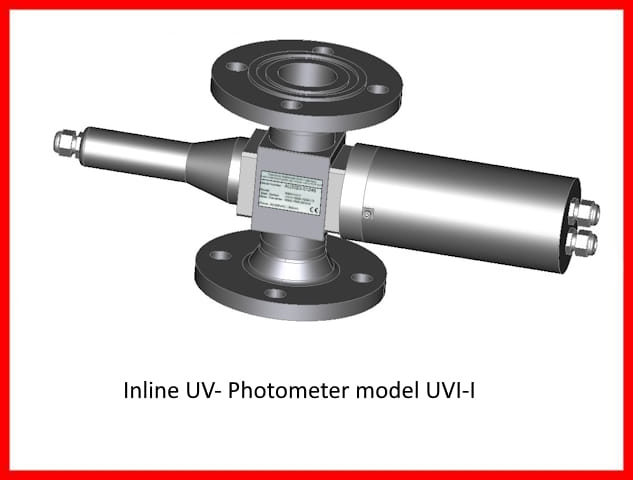
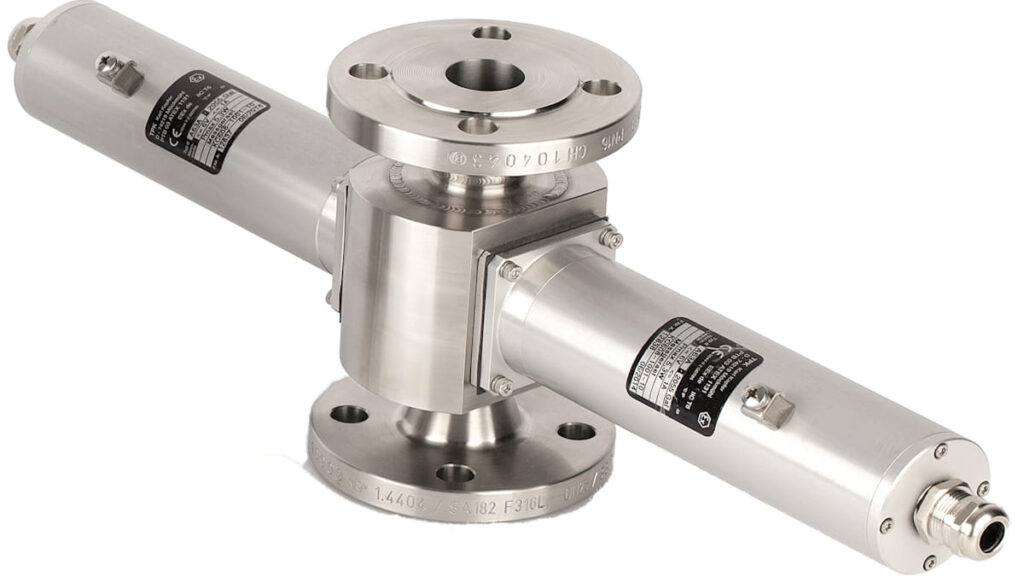
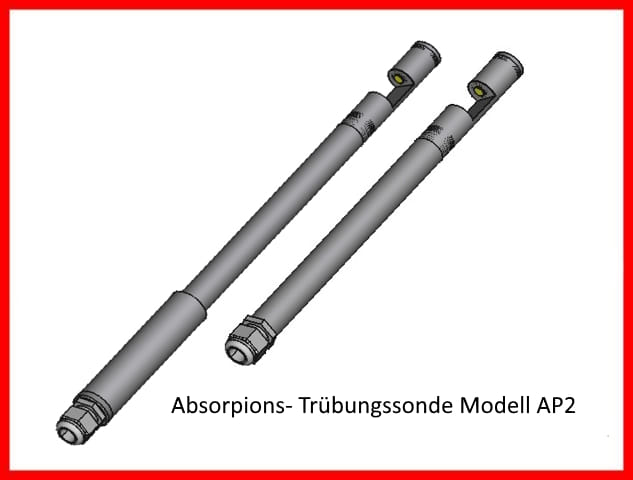
Sensormaterialien moderner Prozessphotometer
Um die Anforderungen Ihrer Anwendung zu erfüllen, werden die medienberührten Teile unserer Prozessmessgeräte je nach Anforderung aus unterschiedlichen Materialien gefertigt. In diesem Abschnitt finden Sie eine Auflistung der gebräuchlichen Sensormaterialien sowie deren Eigenschaften.
Rostfreier Stahl
Rostfreier Stahl als Sensormaterial, auch bekannt als Nirosta, ist ein allgemeinsprachlicher Ausdruck für rost- und säurebeständigen Stahl. Dieser Stahl zeichnet sich durch einen Anteil von mindestens 10,5 bis 13 Prozent Chrom aus, der im austenitischen oder ferritischen Mischkristall gelöst sein muss.
Der Effekt beruht darauf, dass sich durch diesen hohen Chromanteil eine schützende und dichte Passivschicht aus Chromoxid an der Werkstoffoberfläche ausbildet. Weitere Legierungsbestandteile wie Nickel, Molybdän, Mangan und Niob führen zu einer noch besseren Korrosionsbeständigkeit oder günstigeren mechanischen Eigenschaften. Da Chrom als Legierungselement allgemein günstiger ist als Nickel, wird ein höherer Chromanteil bei kleinerem Nickelanteil (gleiche Korrosionsbeständigkeit vorausgesetzt) bevorzugt.
Korrosionsverhalten
Rostfreier Stahl kann unter gewissen Rahmenbedingungen, z. B. in der chlorgashaltigen Luft in Hallenbädern oder im Offshorebereich, durchaus erhebliche Korrosionserscheinungen zeigen (Spannungsrisskorrosion). Hier ist die richtige Werkstoffwahl (Zusammensetzung der Legierung) von entscheidender Bedeutung. Meist erreicht man die Beständigkeit in chloridhaltigen Medien durch Zulegieren von mindestens 2 Prozent Molybdän (z. B. X2CrNiMnMoNbN25-18-5-4). Edelstahl wie X5CrNi18-8 ist bei bestimmten Säuren, etwa Salzsäure (34 %), nicht beständig.
Das Metall löst sich mit der Zeit völlig auf. Seit der Patenterteilung auf Stähle mit „hoher Widerstandskraft gegen Korrosion“ im Jahr 1912 durch die Firma Friedrich Krupp AG in Essen hat die Produktion von rostfreiem Stahl einen gewaltigen Aufschwung genommen.
Auslöser für die Entwicklung eines solchen Stahls war die aufstrebende chemische Industrie im Deutschen Reich. Die damaligen Syntheseverfahren mit Heißdampf, säurehaltigen Medien und sehr hohen Temperaturen ließen herkömmliche Stähle spröde (Wasserstoffsprödigkeit) und rissig werden. Viele damalige Reaktoren waren bis dato aus Granit gefertigt, um diese Nachteile zu umgehen.
Die 1913 anlaufende Ammoniaksynthese (Haber-Bosch-Verfahren) konnte nur durch den Einsatz von austenitischen CrNi-Stählen, wie sie Krupp ein Jahr zuvor entwickelt hatte, realisiert werden. Die parallele Entwicklung der Stahl- und Chemieindustrie, insbesondere dieser beiden Ereignisse, war deshalb kein Zufall.
Eigenschaften und Anwendung
Obwohl sich die meisten rostfreien Stähle nur sehr schlecht zerspanen lassen, bietet ihr Einsatz als Sensormaterial überwiegend Vorteile. Hier sind beispielsweise neben hygienischen Aspekten auch die Langlebigkeit der produzierten Teile und Vorteile im Umweltschutz zu nennen. Nachteil gegenüber anderen Stählen ist jedoch die zumeist geringe Zugfestigkeit und oft fehlende Härtbarkeit.
Bemerkenswert ist auch die im Vergleich zu Kupfer und seinen Legierungen geringere antibakterielle Wirkung. Dazu ein US-amerik. Testergebnis, auch bekannt als oligodynamischer Effekt (Oligodynamie). Weitere Vorteile sind UHV-Dichtheit von Schweiß-Verbindungen und geringer Magnetismus. Für Werkzeuge und Messer werden jedoch härtbare martensitisch-ferritische Stähle verwendet, die neben Chrom oft auch Vanadium und Molybdän enthalten und magnetisch sind. Typische Stahlsorten hierfür sind X30Cr13 und die hochwertigere Legierung X50CrMoV15 (vgl. Messerstahl).
Im Offshorebereich finden auch ferritisch-austenitische Duplex-Stähle, z. B. 1.4462 (X2CrNiMoN22-5-3) Anwendung. Anstelle von Nickel kann für austenitische Stähle auch das billigere Mangan als Legierungselement verwendet werden, aber die allgemeine Qualität dieser Stähle ist niedriger. Für den Offshorebereich sind Bauteile aus dem Sonderwerkstoff X2CrNiMoN17-13-5 (Werkstoffnummer 1.4439/Alloy 317 LN) zu bevorzugen. Schraubenwerkstoffe aus nichtrostenden Stählen und deren Bezeichnungen sind in der EN ISO 3506 genormt.
Beim Ersetzen von Schrauben mit konventionellem Werkstoff durch Niro-Schrauben ist zu beachten, dass die Werkstoffkennwerte (Zugfestigkeit, Bruchdehnung, Dehngrenze etc.) dieser Niro-Schrauben meist unter denen konventioneller Schrauben mit Festigkeitsklasse größer gleich 5.6 liegt. Ein einfaches Ersetzen nach dem 1:1-Prinzip ist gerade bei sicherheitsrelevanten Verbindungen genau zu prüfen.
Normierung
In der europäischen Norm DIN EN 10088, Teil 1-3 sind die technischen Lieferbedingungen für nichtrostende Stähle allgemein geregelt. Zum Abschätzen der Korrosionsbeständigkeit eines rostfreien Stahls kann die Wirksumme (auch PRE-Wert) dienen. Je höher diese ist, desto beständiger ist die Legierung gegen Lochfrass oder Spaltkorrosion. Legierungen mit einer Wirksumme über 33 gelten als seewasserbeständig.
International Organization for Standardization: ISO im Internet
Deutsches Institut für Normung E. V.: DIN/EN im Internet
Interkristalline Korrosion
Die Beständigkeit gegenüber Korrosion sinkt mit steigendem Kohlen-. stoffgehalt, da Chrom eine hohe Kohlenstoffaffinität besitzt und sich hartes, sprödes Chromkarbid vorwiegend an den Korngrenzen bildet, zu Lasten von schützendem Chromoxid. Außerdem neigen dann die Stähle zur inter- kristallinen Korrosion. Um diesem Effekt entgegenzuwirken und damit auch die Schweißbarkeit zu verbessern, wird der Kohlenstoffgehalt niedrig gehalten und die entsprechenden Stahlsorten noch durch Zugabe von Niob oder Titan (die eine höhere Affinität zum Kohlenstoff als Chrom haben), stabilisiert.
Übersicht der WerkstoffbezeichnungenIn der Tabelle sind die allgemeinen nichtrostenden und säurebeständigen Stähle aufgelistet. |
EN-NormWerkstoff-Nr | EN-NormKurzname | ASTM/AISIBezeichnung | UNSBezeichnung |
1.4016 | X6Cr17 | 430 | |
1.4512 | X2CrTi12 (alt X6 CrTi 12) | 409 | |
1.4310 | X10CrNi18-8 (alt X12 CrNi17 7) | 301 | |
1.4318 | X2CrNiN18-7 | 301LN | |
1.4307 | X2CrNi18-9 | 304L | S30403 |
1.4306 | X2CrNi19-11 | 304L | S30403 |
1.4311 | X2CrNiN18-10 | 304LN | S30453 |
1.4301 | X5CrNi18-10 | 304 | S30400 |
1.4948 | X6CrNi18-11 | 304H | S30409 |
1.4303 | X4CrNi18-12 (alt X5 CrNi18 12) | 305 | S30500 |
1.4541 | X6CrNiTi18-10 | 321 | S32100 |
1.4878 | X10CrNiTi18-10 (alt X12 CrNiTi18 9) | 321H | S32109 |
1.4404 | X2CrNiMo17-12-2 | 316L | S31603 |
1.4401 | X5CrNiMo17-12-2 | 316 | S31600 |
1.4406 | X2CrNiMoN17-11-2 | 316LN | S31653 |
1.4432 | X2CrNiMo17-12-3 | 316L | S31603 |
1.4435 | X2CrNiMo18-14-3 | 316L | S31603 |
1.4436 | X3CrNiMo17-13-3 | 316 | S31600 |
1.4571 | X6CrNiMoTi17-12-2 | 316Ti | S31635 |
1.4429 | X2CrNiMoN17-13-3 | 316LN | S31653 |
1.4438 | X2CrNiMo18-15-4 | 317L | S31703 |
1.4539 | X1NiCrMoCu25-20-5 | 904L | N08904 |
1.4547 | X1CrNiMoCuN20-18-7 | S31254 |
Hastelloy als Sensormaterial
HASTELLOY® Alloy C-22 -ein vielseitig anwendbarer Werkstoff für die chemische Industrie. HASTELLOY ist ein eingetragener Handelsname der Cabot Corporation, Boston, MA Der HASTELLOY®-Legierung C-22 liegt eine kritische Abstimmung der Legierungs-elemente Chrom, Molybdän und Wolfram zu Grunde.
Dieses Verhältnis bewirkt eine optimale Korrosionsbeständigkeit im Ni-Cr-Mo-System gegen oxiderende und nicht-oxidierende Säuren sowie gegen Loch- und Spaltkorrosion. Legierung C-22 verfügt darüber hinaus über eine ausgezeichnete thermische Stabilität bei Schweißverfahren mit hohem Wärmeeinbringen.
Die bisherigen Anwendungen von HASTELLOY alloy C-22 bestätigen, daß dieser Werkstoff schwierige Korrosionsprobleme in der Praxis selbst dort löst, wo andere hochkorrosionsbeständige Legierungen versagen. Die Legierung wird für den Bau von Druckbehältern verwendet, die im Temperaturbereich zwischen -196°C und 400°C eingesetzt werden. Im Hinblick auf diese Anwendung sind mechanische Eigenschaften und Verarbeitungsdaten bestimmt worden. Hastelloy alloy C-22 ist in seinem mechanischen Verhalten den anderen Legierungen des C-Typs vergleichbar.
Der Werkstoff besitzt eine hohe Zähigkeit bei niedrigen Temperaturen, selbst im kaltumformten Zustand. Er ist gut schweißbar und kommt daher häufig als Sensormaterial bei Chloridhaltigen Produkten zum Einsatz.
Titan
Titan ist ein chemisches Element im Periodensystem der Elemente mit dem Symbol Ti und der Ordnungszahl 22.
Es gehört zu den Übergangsmetallen. Leicht, fest, dehnbar, weiß-metallisch glänzend und korrosionsbeständig ist es besonders als Sensormaterial für Anwendungen geeignet, bei denen es auf hohe Korrosionsbeständigkeit, Festigkeit und geringes Gewicht ankommt.
Geschichte:
Titan wurde 1791 in England durch den Geistlichen und Amateurchemiker William Gregor im Titaneisen entdeckt. Mehrere Jahre später entdeckte es der deutsche Chemiker Heinrich Klaproth im Rutilerz erneut. 1795 benannte er das neue Element Titan. Reines Titanmetall (99,9 %) stellte 1910 erstmals Matthew A. Hunter her, indem er in einer Stahlbombe Titantetrachlorid mit Natrium auf 700 bis 800 °C erhitzte. Erst die Einführung der großtechnisch durchgeführten Reduktion von Titantetrachlorid mit Magnesium (Kroll-Prozess durch William Justin Kroll 1946) erschloss das Titan für kommerzielle Anwendungen.
Eigenschaften:
Titan bildet an Luft eine äußerst beständige oxidische Schutzschicht aus, die es in vielen Medien korrosionsbeständig macht. Bemerkenswert ist die hohe Festigkeit bei einer relativ geringen Dichte. Oberhalb einer Temperatur von 400 °C gehen die Festigkeitseigenschaften aber schnell zurück. Hochreines Titan ist duktil.
Bei höheren Temperaturen versprödet es durch Aufnahme von Sauerstoff, Stickstoff und Wasserstoff sehr schnell. Zu beachten ist auch die hohe Reaktivität von Titan mit vielen Medien bei erhöhten Temperaturen oder erhöhtem Druck, wenn die Passivschicht dem chemischen Angriff nicht gewachsen ist. Hier kann die Reaktionsgeschwindigkeit bis zur Explosion anwachsen. In reinem Sauerstoff bei 25 °C und 25 bar verbrennt Titan von einer frischen Schnittkante ausgehend vollständig zum Titandioxid.
Bei Temperaturen oberhalb von 880 °C reagiert es mit Sauerstoff, bei Temperaturen ab 550 °C mit Chlor trotz Passivierungsschicht. Titan reagiert („brennt“) auch mit reinem Stickstoff, was bei Hitzeentwicklung wie zum Beispiel bei spanender Bearbeitung unbedingt beachtet werden muss. In verdünnter Schwefelsäure, Salzsäure, chloridhaltigen Lösungen und den meisten organischen Säuren ist Titan beständig. Wegen der Explosionsgefahr sind bei Anwendungen in Chlorgas die Betriebsbedingungen strikt einzuhalten.
Monel
Monel, auch Monelmetall genannt, nach Ambrose Monel († 1921), ist eine Nickel-Kupfer-Legierung (ungefähr: 65% Nickel, 33% Kupfer und 2% Eisen) mit hoher Zugfestigkeit, die sich sehr beständig gegenüber atmosphärischer Korrosion, Meerwasser und einer Vielzahl von Säuren und alkalischen Lösungen verhält.
Die Bezeichnung Monel ist ein geschützter Markenname der Firma Special Metals Corporation, Huntington (West Virginia), USA.
Das Material gilt als ein Vorläufer des rostfreien Stahls. Monel wird in der Schiffstechnik, für den Turbinenbau, für Ausrüstungen in der Chemie- und Kohlenwasserstoffindustrie, für Ventile, Pumpen und Wärmeübertrager verwendet. Es ist bemerkenswert stabil gegenüber dem aggressiven Fluor F2 (Passivierung der Moneloberfläche durch Fluorierung) und wird deshalb als Material für F2-Aufbewahrungs-gefäße (Druckflaschen) verwendet.
TFM™ PTFE als Sensormaterial
TFM™ PTFE ist ein verzweigtes Polymer, mit der Formel:
—[(CF2)4- CF(-O-CF2-CF2-CF3) — (CF2)5]n—
Die perfluorierte Seitengruppe ist identisch mit derjenigen von PFA, jedoch in deutlich geringeren Mengen enthalten. Das Molekulargewicht beträgt nur ca. 1/5 desjenigen von PTFE während PFA nur 1/100 des Molekulargewichts von PTFE besitzt. Daher füllt es die “Eigenschaftslücke“ zwischen PTFE und PFA ohne dass es wie PFA in einem Spritzgussverfahren verarbeitet werden muss. Eigenschaften TFM™ PTFE ist temperaturbeständig von -200° bis +250°C im Dauerbetrieb.
Chemische Beständigkeit:
TFM™ PTFE Ist absolut chemikalienbeständig daher fast universell einsetzbar. Die Permeationsrate von Gasen durch TFM™ PTFE ist deutlich geringer als durch herkömmliches PTFE und nur unwesentlich höher als durch PFA.
Sonstige Eigenschaften:
Die Oberflächenbeschaffenheit von TFM™ PTFE ist gegenüber PTFE deutlich verbessert außerdem ist das Material nach speziellen Methoden verschweißbar, eine Folge der „Verschiebung in Richtung Thermoplast“. TFM™PTFE hat einen verbesserten Kaltfluß, Porengehalt und Stretch-Void-Index. TFM™PTFE kann mit organischen Stoffen wie Glasfaser, Graphit, Kohle gemischt werden (Compounds). Dadurch können die Eigenschaften wesentlich verändert werden, vor allem die Druckfestigkeit, die Wärmedehnung, die elektrischen Werte und der Abrieb. Bei Zusatz von Kohlenstoff wird z.B. der elektrische Widerstand des Materials soweit abgesenkt das es sich ohne die Gefahr von statischer Aufladung innerhalb von explosionsgefährdeten Bereichen einsetzen lässt.
PVDF als Sensormaterial
PVDF wurde im Jahr 1961 unter dem Markennamen „Kynar“ von der Pennwalt Corp. in den Handel gebracht.
Einsatzgebiete:
1969 wurde von Kawai der piezoelektrische Effekt von PVDF entdeckt. Wegen seiner guten thermischen und chemischen Beständigkeit wird PVDF als Auskleidung für Rohre oder Außenbauteile eingesetzt. Außerdem wird es für Dichtungen, Membranen und Verpackungsfolien verwendet. Weiterhin findet es auch Anwendung in der Messtechnik, z. B. beim Beschichten von Messsonden. Da das Material starke piezoelektrische Effekte zeigt, wird es auch in Mikrophonen, Hydrophonen, Lautsprechern und Aktuatoren eingesetzt.
Eigenschaften:
Verhalten bei Strahlenbelastung PVDF besitzt eine gute Beständigkeit gegen UV- und Gammastrahlung. PVDF ist daher sehr alterungsbeständig. Physiologische Unbedenklichkeit PVDF eignet sich gemäß FDA „Title 21, Code of Regulations (USA) Chapter 1, part 177.2510“ für die sichere Verwendung für Gegenstände, die für wiederholten Kontakt mit Nahrungsmitteln bestimmt sind. PVDF ist zugelassen für den Einsatz in Verarbeitungsanlagen und Lagervorrichtungen des „US-Department of Agriculture (USDA)“.
Hygiene:
PVDF entspricht auch den Kriterien der „3-A Sanitary Standards for Multiple-Use Plastic Materials Used as Product Contact Surfaces for Dairy Equipment, Serial-No.2000“. Vermehrung von Mikroorganismen auf PVDF Die Oberfläche aus PVDF bildet für die Vermehrung von Mikroorganismen einen ebenso ungünstigen Nährboden wie Glas. So lautet das Schlußergebnis einer Untersuchung, die Solvay von „Centre d‘ Enseignement et de Recherches des Industries Alimentaires et Chimiques“ (CERIA in Brüssel) durchführen ließ. Aufgrund dieser Eigenschaften wird PVDF in der Lebens-mittelindustrie (z.B. in Molkereien) wie auch in der pharmazeutischen Industrie (z.B. für sterilisierbare Präzisionsdosierpipetten) und im Reinst-medienbereich der Halbleiterindustrie eingesetzt.
Chemische Beständigkeit:
PVDF hat eine bemerkenswerte Widerstandsfähigkeit gegen die meisten anorganischen und organischen Säuren, oxydierende Medien, aliphatische und aromatische Kohlenwasserstoffe, Alkohole und halogenhaltige Lösemittel. Es widersteht Halogenen – insbesondere Brom (aber nicht Fluor) – und schwachen Laugen. Es wird abgebaut von rauchender Schwefelsäure, einigen stark basischen Aminen, konzentrierten und heißen Alkalien sowie Alkalimetallen. In stark polaren Lösemitteln, wie Aceton und Ethylacetat, quillt es und ist etwas löslich in aprotischen Lösemitteln wie Dimethyl-formamid und Dimethyl-sulfoxid.
VICTREX® PEEK™ als Sensormaterial
Polymer Hochleistungsthermoplast mit außergewöhnlichen Eigenschaften.
VICTREX PEEK Polymer ist ein aromatischer, teilkristalliner Thermoplast aus der Gruppe der Polyaryletherketone (PAEK). Er lässt sich mit allen üblichen thermoplastischen Verfahren verarbeiten und zeichnet sich durch die Kombination hervorragender Eigenschaften aus: ausgezeichnete chemikalienbeständigkeit, exzellente tribologische, thermische, elektrische und mechanische Eigenschaften sowie Dimensionsstabilität.
PEEK verfügt über:
- eine Dauergebrauchstemperatur von +250°C, kurzzeitig bis +300°C
- hervorragende mechanische Eigenschaften
- ausgezeichnete Chemikalien- und Strahlenbeständigkeit
- Hydrolysebeständigkeit
- kein Ausgasen im Vakuum
- sehr gute tribologische Eigenschaften
- Lebensmittelechtheit
Wie bereits erwähnt, erhalten Formteile aus PEEK ihre außergewöhnlich guten mechanischen Eigenschaften über lange Zeitspannen und bei sehr hohen Temperaturen weitestgehend bei und ist darum als Sensormaterial für viele anspruchsvolle Anwendungen geeignet.